pravin b
Member level 5
- Joined
- May 20, 2012
- Messages
- 85
- Helped
- 2
- Reputation
- 4
- Reaction score
- 1
- Trophy points
- 1,288
- Location
- Mumbai, India
- Activity points
- 2,083
Hello friends,
I am trying to design an instrumentation amplifier using LM324 (since it works with single power supply (as per datasheet), it is cheap and available in stock). However currently I am testing my circuit on proteus, but I am not getting the calculated gain &/or output using single power supply. whereas I am getting the calculated gain if dual supply to opamp is used. It would be helpful if someone can shed some light on this and suggest the modification to use it on single power supply.
Here is my circuit for reference.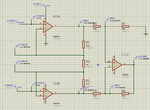
I am trying to design an instrumentation amplifier using LM324 (since it works with single power supply (as per datasheet), it is cheap and available in stock). However currently I am testing my circuit on proteus, but I am not getting the calculated gain &/or output using single power supply. whereas I am getting the calculated gain if dual supply to opamp is used. It would be helpful if someone can shed some light on this and suggest the modification to use it on single power supply.
Here is my circuit for reference.
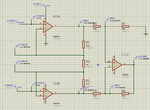