pasau
Newbie level 5
i have a SMPS power supply, very similar to the one found at page 30 on this document:
my goals are to obtain:
flyback configuration
Here is my circuit
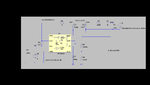
- I added primary and secondary ESR, based on the measurements i made from my inductance
when doing a spice3 transient simulation, i get this:
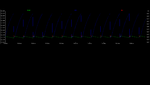
green is Vout, blue is Iprimary and red is Isecondary. The primary current goes up to 0.9A in this simulation, which is well within the maximum allowed by my MC34063 controller
So everything works fine in simulation; i use a current source as my load to have better control, but same result with spice resistance. I put initial condition to get to steady state faster otherwise simulation takes a lot of time.
My goal is to have a ratio of 1:10 on my flyback transformer to boost the output voltage, since the chip cannot support an output voltage of more than 40V directly
In practice, i use an EP7-3E6 ferroxcube, with 2 windings.
the main specifications are:
According to some theory, the Al factor of 5.8uH means the henries per turn squared: 5.8uH/N^2, which means at the primary, i have sqrt(145/5.8) = 5 turns.
at the secondary, i have sqrt(13000/5.8) ~= 50 turns
in practice, the 145uH and the 13mH were measured, after i did my windings manually, with 6 turns with 30 AWG at the primary, and 60 turns of 38 AWG at the secondary. So basically, it seems close enough to the 5/50 turns i shouldve needed according to the specs.
The problem is that when measuring the output voltage, with the required load for the 3mA current i am expecting, i get some much lower voltage, like ~50V. Also, i noticed that the chip MC34063 heats a lot, which makes me think that the current goes beyond the expected 0.9A in the primary, and also above the maximum of 1.5A.
Since everything else seems to be modeled correctly in my spice simulation, i think the problem is related to my flyback transformer. I am new to magnetics, so i would like to have the opinion of someone who knows the main problems you can get when attempting this sort of circuit.
Thanks!
my goals are to obtain:
flyback configuration
Vin=9V
Vout=180V
Iout=3mA
Vout=180V
Iout=3mA
Here is my circuit
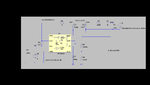
- I added primary and secondary ESR, based on the measurements i made from my inductance
when doing a spice3 transient simulation, i get this:
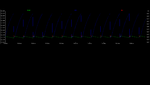
green is Vout, blue is Iprimary and red is Isecondary. The primary current goes up to 0.9A in this simulation, which is well within the maximum allowed by my MC34063 controller
So everything works fine in simulation; i use a current source as my load to have better control, but same result with spice resistance. I put initial condition to get to steady state faster otherwise simulation takes a lot of time.
My goal is to have a ratio of 1:10 on my flyback transformer to boost the output voltage, since the chip cannot support an output voltage of more than 40V directly
In practice, i use an EP7-3E6 ferroxcube, with 2 windings.
the main specifications are:
- Ae Effective Cross Scetion Area: 10.7mm²
- Core Material Grade: 3E6
- Core Size: EP7
- Effective Magnetic Path Length: 15.5mm
- For Use With: -
- Inductance Factor Al: 5.8µH
- SVHC: No SVHC (17-Dec-2015)
According to some theory, the Al factor of 5.8uH means the henries per turn squared: 5.8uH/N^2, which means at the primary, i have sqrt(145/5.8) = 5 turns.
at the secondary, i have sqrt(13000/5.8) ~= 50 turns
in practice, the 145uH and the 13mH were measured, after i did my windings manually, with 6 turns with 30 AWG at the primary, and 60 turns of 38 AWG at the secondary. So basically, it seems close enough to the 5/50 turns i shouldve needed according to the specs.
The problem is that when measuring the output voltage, with the required load for the 3mA current i am expecting, i get some much lower voltage, like ~50V. Also, i noticed that the chip MC34063 heats a lot, which makes me think that the current goes beyond the expected 0.9A in the primary, and also above the maximum of 1.5A.
Since everything else seems to be modeled correctly in my spice simulation, i think the problem is related to my flyback transformer. I am new to magnetics, so i would like to have the opinion of someone who knows the main problems you can get when attempting this sort of circuit.
Thanks!