Hicham M
Member level 1
Hello,
I have a device that reads CAN bus information, but today the device doesn't work anymore.
I opened the device and started debugging it ( I have the schematic ).
The following schematic is the part for CAN.
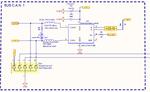
CAN1_RX, CAN1_TX goes straight to a microcontroller.
I found that the dioes in D25 : D5 (between4-2) and D6(between6-2) are broken.
the PESD5V0L5UY is a Low capacitance unidirectional fivefold ElectroStatic Discharge (ESD) protection diode.
now, i'm basically a software developper, so I only have basics in electronics.
My question is : what could make these 2 diodes burned out like that ?
I admit that I messed around with the board. any advice how to avoid that next time ?
and I also noticed that the Vcl of the PESD5V0L5UY is 12V image below
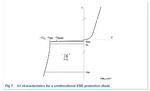
I'm using a power supply of 24V, could this be the reason of my problem ??
I have a device that reads CAN bus information, but today the device doesn't work anymore.
I opened the device and started debugging it ( I have the schematic ).
The following schematic is the part for CAN.
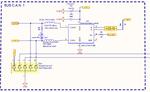
CAN1_RX, CAN1_TX goes straight to a microcontroller.
I found that the dioes in D25 : D5 (between4-2) and D6(between6-2) are broken.
the PESD5V0L5UY is a Low capacitance unidirectional fivefold ElectroStatic Discharge (ESD) protection diode.
now, i'm basically a software developper, so I only have basics in electronics.
My question is : what could make these 2 diodes burned out like that ?
I admit that I messed around with the board. any advice how to avoid that next time ?
and I also noticed that the Vcl of the PESD5V0L5UY is 12V image below
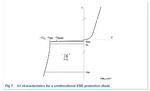
I'm using a power supply of 24V, could this be the reason of my problem ??