Instructor
Newbie level 6
Good Day. I need to switch from a Darlington for a car ignition coil to MOSFET.
The Darlington needs a huge Heat sink while the MOSFET trial did not.
I just want to confirm the circuit and checking if there might be any error with the MOSFET. Can you please help?
Attached are both circuits, the old and the new.
Thank you.
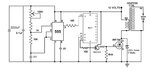
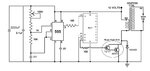
The Darlington needs a huge Heat sink while the MOSFET trial did not.
I just want to confirm the circuit and checking if there might be any error with the MOSFET. Can you please help?
Attached are both circuits, the old and the new.
Thank you.
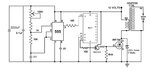
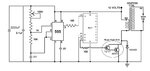