mshh
Full Member level 6
i want to drive proportional valve from a plc .the valve specs is 24V 1.5Amp. the output from plc is 0-10V , i will amplify it to 0-24 v . now the problem in driving phase . if i apply the amplified signal , the transistor will get hot. so i think that pwm will be used .
i propose the attached sketch . using a comparator will control the current of the mosfet by controlling the width of the duty cycle ,when the input signal changed from 0-24V. i put R1 to control max voltage consequently max current in the valve . i think now we don't need heatsink.
need your comment
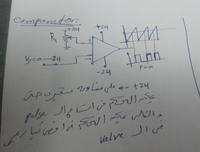
i propose the attached sketch . using a comparator will control the current of the mosfet by controlling the width of the duty cycle ,when the input signal changed from 0-24V. i put R1 to control max voltage consequently max current in the valve . i think now we don't need heatsink.
need your comment
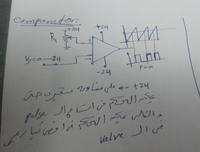