bhl777
Full Member level 6
Hi All, I have an open loop wireless power transfer system. I use a class E power amplifier to drive the Tx coil. In the Rx side I have a rectifier to generate an output DC voltage.
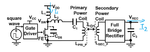
Would anyone teach me how to implement an easiest closed loop regulation of this WPT system? Ideally I want to use some analog components (such as the op-ampm, instead of the microcontroller or any other programming logic circuits) to achieve a ceratin level of the V_REC voltage regulation. The regulation is not necessarly perfect, but the feedback loop must use the same Tx and Rx coils. Is it possible to design such a loop?
Thank you!
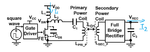
Would anyone teach me how to implement an easiest closed loop regulation of this WPT system? Ideally I want to use some analog components (such as the op-ampm, instead of the microcontroller or any other programming logic circuits) to achieve a ceratin level of the V_REC voltage regulation. The regulation is not necessarly perfect, but the feedback loop must use the same Tx and Rx coils. Is it possible to design such a loop?
Thank you!